River sand stone crushing and washing plant
Basic information
● Material, river sand and gravels, mostly 0-150mm
● Feeding capacity 80 tons per hour, half sand
● Mesh size, 5mm, 3/8'', 3/4'', 1’’, products sand, 3/8’’, 3/4’’, G1 and above
● Diesel generator set drive the whole plant
Screening & crushing in details
1. Raw materials loading and separation
All raw materials are loaded to a grizzly hopper, grizzly bar distance 150mm, large than 150mm will be separated. Under the hopper, a vibrating feeder is installed, it is heavy duty feeder, which requires little or no maintenance.
There is minimal risk of downtime and parts are simple to replace. It controls the materials flow rate, a stable and continuous feeding is always good for complete plant, also for the stable supply of electricity by diesel generator set.
2. Screening, crushing and washing
All the materials are sent to a 4 layer vibrating screen for separation, mesh size 5mm, 10mm, 19mm and 25mm.
Above the vibrating screen, high pressure water sprays are added. Washing is performed by applying water jets through spray nozzles directed as a water curtain and under pressure at the material being washed.
Larger than 25mm will be crushed by a secondary jaw crusher 10x47’’, with C.S.S. 30mm, it gets gravel less than 40mm. Mainly G1 to 40mm. The crushed gravel is sent to stockpile 1, this is product 1
19 to 25mm will be conveyed to stockpile 2, this is product 2
10 to 19mm will be conveyed to stockpile 3, this is product 3
5 to 10mm will be conveyed to stockpile 4
Less than 5mm, which accounts for about 60% of total materials are collected by a hopper and steel chute, by gravity and water slurry on the screen, they flow to the wheel sand washer. After washing, it gets clean sand and conveyed to stockpile 5.
Features
1. Simple design, low investment, less power needed
2. Diesel generator set to power the whole plant, workable in remote mining area
3. Reasonable design and heavy duty equipment guarantee stable production, less shutdown time
4. Deya Machinery offers full service from A to Z, consulting, designing, quotation sheet, production, delivery, installation, commissioning and training.
5. Automatic running, all equipment are controlled by electrical panels
Contact Deya Machinery team to customize the crushing and screening plant for you.
Photos from the crusher plant working site, installation to production
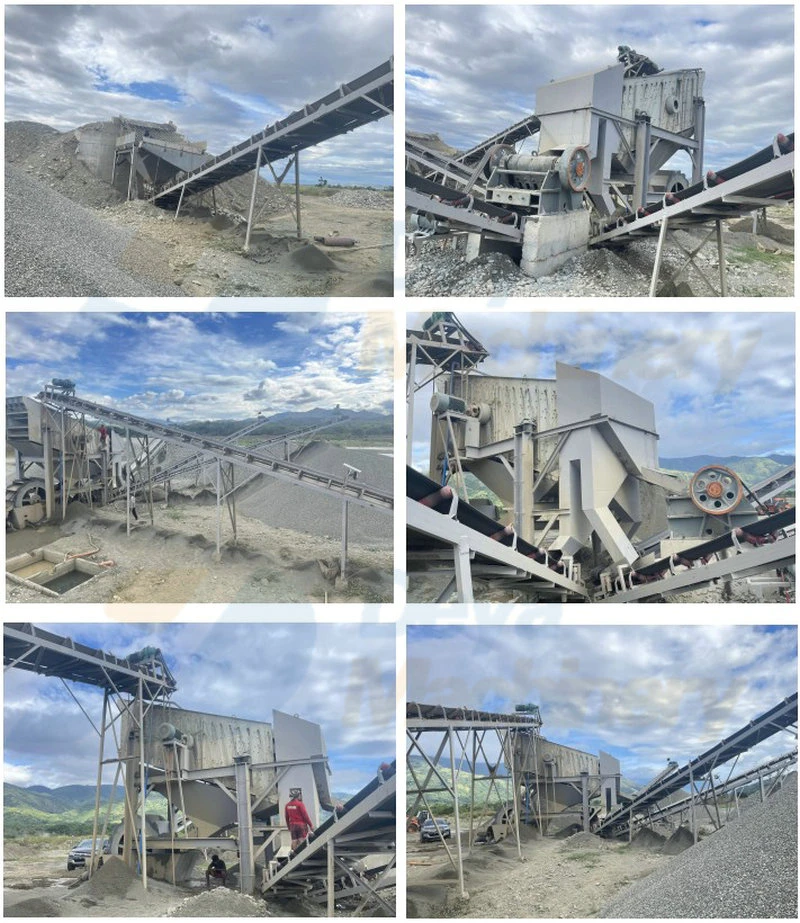