Wet drum magnetic separator
Technical Details
The Wet Drum Magnetic Separator recovers magnetite and ferrosilicon in dense media plants for iron ore beneficiation, it is also used for the scrap recycling and coal processing industries.
The Wet Drum Magnetic Separator features a strong, stationery permanent magnetic element mounted inside a revolving non-magnetic shell.
The adjustable multi-pole ceramic ferrite magnetic element produces a high-flux, radial magnetic field, along the circumference of the shell, which maximises recovery to + 99.9%.
Magnetite recovery commonly occurs in coal washing plants with ferro-silicon recovery an important stage in the heavy-media separation of secondary metals in scrap metal fragmentation plants.
The Wet Drum Magnetic Separator is a key part of a dense media plant, located after the density separation process to recover the heavy media (magnetite or ferrosilicon) for recycling and reuse.
High percentage recoveries are vitally important due to the high cost of the media. Multiple stages of Wet Drum Magnetic Separation feature in coal washing plants and secondary metal heavy-media operations.
Magnet System
This is the most critical part of any wet drum design; the permanent magnet unit involves the use of strontium or barium ferrite non-deteriorating ceramic magnets enclosed in stainless steel cases.
The wet drum separators have a multi-pole high flux gradient and Gauss value, ensuring maximum adhesion of magnetics to drum cover whilst tumbling the magnetics and releasing entrapped non-magnetics as the product passes over alternate (N/S) stationary poles within the drum.
This ensures a clean magnetic product and minimum entrainment of non- magnetic and colloidal material. The magnet system within the drum is adjustable radially to ensure the optimum setting for magnetics recovery and solids density and by shims allowing minimum clearance between drum cover and magnet, bringing the magnet poles as close as possible to the media slurry, ensuring maximum magnetic field strength in the separating zone of the unit.
Drum construction
The main cover is in stainless steel, as is the replaceable wearing cover, the drum can be rubber covered if required. Stainless steel end flanges have inner and outer seals ensuring the cover and flange joints are watertight.
Sealed for life proprietary flange bearings have grease nipples fitted and are protected from the slurry running down the flange by a simple radial cover.
An adjustment mechanism on the shaft allows the magnet system to be readily moved to the optimum setting before being locked in position.
Tank & Launder
Manufactured in stainless steel, the two-compartment header box ensures uniform feed to the drum. The launder design depends on the type of process involved. A step feature ensures that the slurry impinges on the drum face directly, where the magnet is the strongest.
Drum Scraper, Spray Pipe and Spill Boxes
• Rubber scraper or an alternative of a spray pipe are fitted depending on application
• Spill boxes for intermediate water supply are fitted when multi-drum installations are used
Principle of Operation
A slurry containing the magnetic component is fed between the rotating magnet drum cover and casing.
The stationary magnet system, which has several radial poles, attracts the magnetic component to the drum face, and the rotating cover carries the magnetics from one magnetic pole to another at the same time, gyrating the magnetic particles and allowing entrapped non-magnetics to fall away back into the slurry mainstream, ensuring a clean magnetic product is discharged clear of the slurry tailings.
Tank Design
There are three basic tank designs:
Concurrent
Concurrent tanks suit applications requiring high recoveries of medium with a high concentrate specific gravity.
Also, the Concurrent design enables the handling of slurry with particles up to 6mm in size.
To maximize the recovery of magnetite or ferrosilicon, two Wet Drums work in series with the tailings from stage 1 feeding into the second Wet Drum.
Counter Flow
The Counter Flow design primarily caters for processes with surges in throughput. The tank configuration minimizes magnetic material losses in slurry with a high magnetics content, especially when a clean concentrate is not of prime importance.
Although the ideal material specification for this design is <0.5mm or -30 mesh with a solids content of 30-40% by weight, the Counter Flow configuration handles materials with particles up to 4mm.
Counter Current
The Counter Current tank produces a high-grade magnetic concentrate, with lost fine magnetics passing into the tailings which are then re-processed to maximize magnetics recovery.
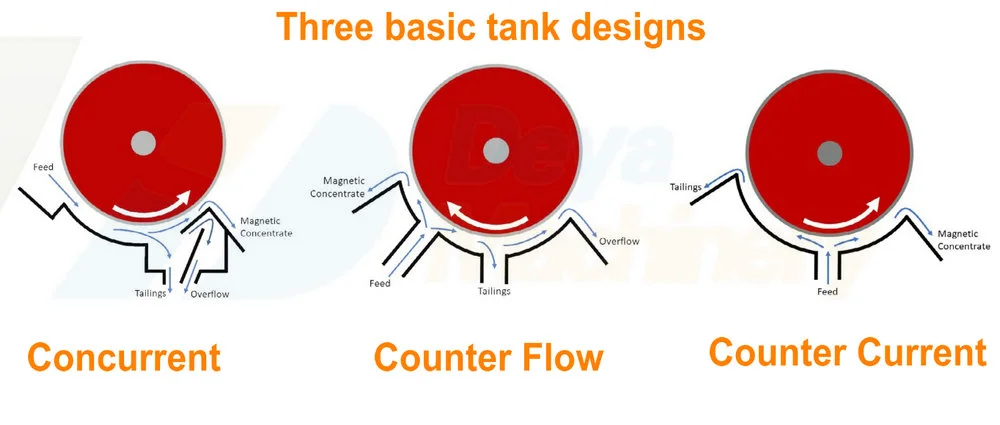
Applications
Wet Drum Magnetic Separators can be used for increased efficiency in the following:
• Heavy media plants for recovery of magnetite or ferrosilicon.
• Iron Ore concentration
• Extracting ferromagnetic material from various slurry.
• Water Treatment Plants
Heavy Media Plants
Wet drum magnetic separators can process both dilute feeds direct from screens and concentrated feeds in coal plants.
Deya Machinery magnetic drums can deal efficiently with the variations in the amount of magnetite that occur due to high or low tonnage of coal in a constant volumetric throughput of slurry.
Magnetic recovery will be influenced by the percentage of solids and particle size distribution of the feed and the percentage of non-magnetics present relative to magnetics.
Maintaining the slurry level whilst operating the separator is also critical, along with limiting surging.
Excellent recovery figures of +99% can be achieved under the correct operating conditions.
Concentrate Specific Gravity
The separator can achieve concentrate-specific gravities for Magnetite 2.1 to 2.2 and ferrosilicon 2.9 to 3.0, but these can be affected by the amount of magnetics present, the position of the magnet element within the drum, which is adjustable, or the level of the slurry passing through the separator.
Magnetic Concentrate Cleanliness
The percentage of magnetics in the feed can influence the cleanliness of the final concentrate as well as the presence of fine clay and colloidal matter, in waste water applications.
Iron Ore Concentration
Special tank designs are available for cobbing, roughing, and finishing operations in single and multiple stages.
Maintenance
As always, equipment from Deya Machinery is designed with the purchaser in mind, being cost-effective initially and having minimum maintenance requirements so that downtime is always kept to a minimum.
Our suggestions, certain items that are subject to wear, such as bearings and expendable covers, are kept in stock.
Always operate the wet drum magnetic separator according to Deya Machinery's manul.