Everything about jaw crusher
Structure
Jaw crushers are used in mines and quarries as primary crushers. A jaw crusher uses compressive force for breaking of particles.
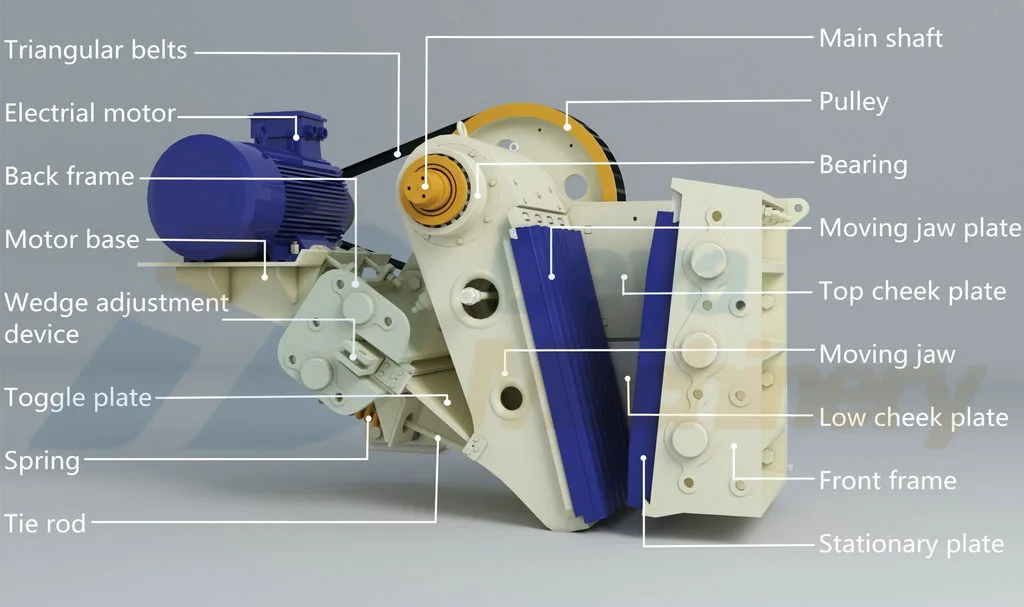
Above figure shows construction of a typical single toggle jaw crusher. It consists of a set of vertical jaws.
The volume or cavity between the two jaws is called the crushing chamber.
The gap between the jaws becomes narrower farther down into the crushing chamber.
One of the jaw is kept stationary and is called a fixed or stationary jaw while the other jaw called a swing or moving jaw, moves back and forth relative to the fixed jaw.
The inertia required to crush the material is provided by a weighted flywheel that moves the eccentric shaft.
Working principle
When the swing jaw moves forward, the pressure required to crush the material is generated because the crushing chamber narrows and the material gets crushed.
When the swing jaw moves back again, the material crushed to the size of the pre-selected jaw opening exits the crushing chamber at the bottom due to gravity while new material flows in from the top.
Jaw Crusher Terms
Feed Opening
It is the distance between the jaws at the feed opening. The feed opening (gape or depth of the cavity) is measured from the top of the tooth of the fixed jaw to the bottom of the tooth of the movable jaw in a straight line perpendicular to the center line of the crushing cavity.
Feed opening defines the maximum feed size of the crusher. The maximum feed size is approximately 80% of the feed opening.
Open Side Setting (OSS)
The open side setting is measured when the crusher is at rest.
The setting is measured either top to top (for closed profile jaw plate, i.e. use of heavy duty jaw plate), or bottom to top (for open profile jaw plates, i. e. jaw plates with tooth), depending on the tooth profile of the jaw plates.
It is the maximum discharge opening/gap.
Throw/Stroke
The throw is stroke of the swing jaw. It is the difference between OSS and CSS.
Closed Side Setting (CSS)
The closed side setting can be calculated by deducting the throw/stroke from the OSS.
CSS is the most important crusher parameter since it defines the maximum product size and has significant bearing on capacity, product gradation, power draw and wear.
It is the minimum discharge opening/gap.
Check the Deya Machinery’s instruction manual for the permitted minimum CSS.
Nip Angle
The nip angle is the angle between the fixed and movable jaw plates.
Too large a nip angle reduces the capacity (due to material squirt out like a large ball which might squirt out from under a car tire) and increases the wear as the feed material grinds and gouges the jaw plates in an upwards direction during the compressive stroke.
Jaw Plates
Replaceable liner plates protecting the jaws from wear.
Cheek Plates
Wear plates used to protect the sides of crusher frame.Toggle plate
In most of the jaw crushers, the toggle plate also serves as a safety mechanism. Should a piece of non-crushable material, generally called tramp iron, enter the jaw crusher and be larger than the bottom opening, it can't be crushed nor pass through the bottom opening.
In this case, the toggle plate will crush and prevent further damage. In some designs, the toggle plate is made up of two steel plates which are bolted together with shear bolts.
Leading
Leading is a technique for measuring the gap between fixed and moveable jaws. The procedure is performed while the crusher is running empty.
As shown in above figure, to measure the gap between the fixed and moveable jaws, a lead wool or aluminum foil ball/plug is lowered in to the jaw crusher up to the discharge opening.
After the crusher has compressed it, it is removed and measured to find out how much thickness remains after its compression. This measurement gives the closed side setting. The open side setting is equal to this measurement plus the throw of the mantle.
Size
Jaw crushers size is specified in terms of the feed opening (gape) and jaw width, typically listed as feed opening x jaw width.Construction Details
A jaw crusher is designed with sacrificial parts to protect the main components of the crusher such as frame and jaws.Crusher Frame and Jaws
Crusher frame and jaws are made of high-grade steel or special cast steel that has been subjected to a stress relieving heat treatment in order to prevent residual stresses from the welding or casting process.
Eccentric Shaft
Eccentric shaft is forged from hardened and tempered alloy steel.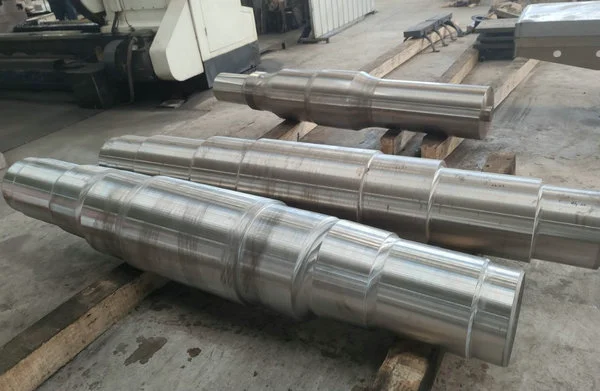
Cheek Plates
Cheek plates are made of high strength special steel.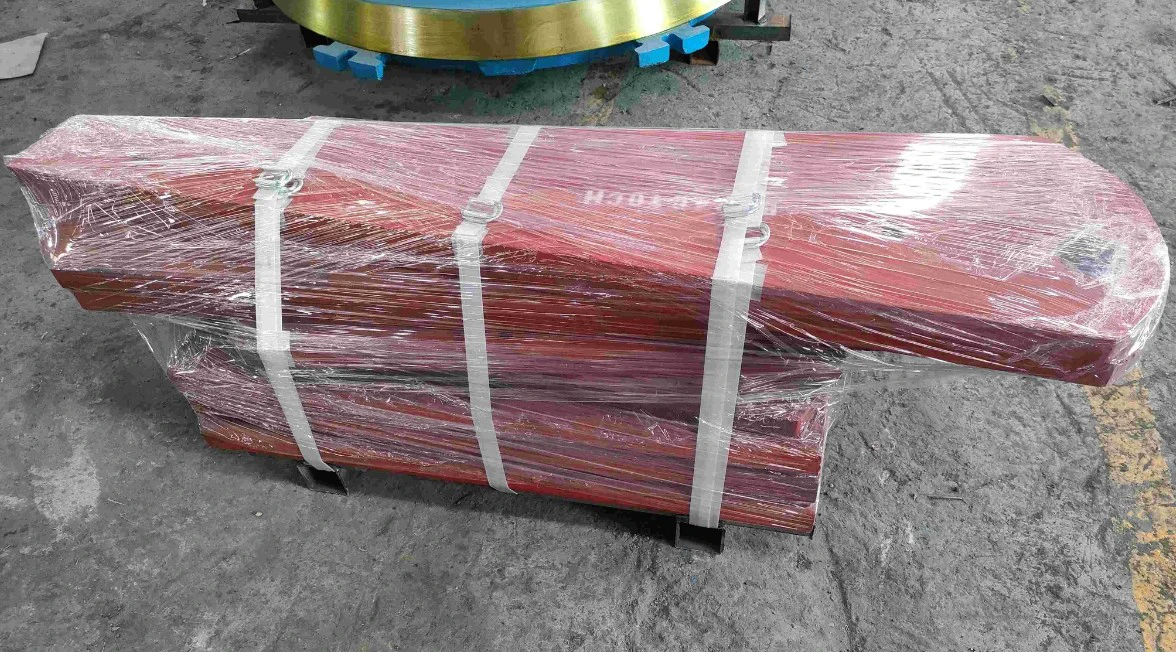
Jaw Plates
Jaw plates are made of high grade austenitic manganese steel.As the earth’s natural resources are becoming scarce, recycling is becoming important.
Recycling of material is generally carried out in the building industry.
Recycling means reuse of demolition concrete, reclaimed asphalt pavement, etc.
Due to the wide range of applications and feed material, jaws plates of many profiles are available.
Above figure shows basic jaw plates profiles and recommendations for their applications.
Different type of jaw plate profiles can be broadly classified in to three categories: sharp teeth (e.g. standard tooth), corrugated teeth (e.g. super tooth) and flat (e.g. heavy duty).
The applicability of these three categories depends on the material being crushed.
Sharp teeth are used for softer materials (hardness below 5 on the Mohs’ hardness scale), corrugated teeth are used for medium hard materials (hardness between 5 and 7 on the Mohs’ hardness scale) and flat profiles are used for very hard rocks (hardness greater than 7 on the Mohs’ hardness scale).
Operation and Maintenance of Jaw Crushers
In order to get optimum capacity and maximum lifetime of wear parts, follow the recommendations given in the operation and maintenance manual provided by Deya Machinery.
Fines (material smaller then CSS) should be removed from the feed material.
This can be done by installing a grizzly feeder.
This reduces wear on the jaw liners and can improve overall plant performance.
Check the feed size. Oversize feed material decreases capacity and can cause unnecessary stresses to the crusher components.
In order to reach optimum capacity and maximize on the life of the wear parts, the crusher cavity/chamber should be full.
Above figure shows the optimum material level. The feed must be distributed evenly across the crushing chamber.
The crusher must not be operated at a smaller CSS than what is stated in the operation and maintenance manual.
A tight CSS will lead to higher wear on jaw plates.
Check the wear profile of the jaw plates. An uneven wear profile will decrease capacity, increase wear, and increase crushing forces.
Maintenance
Check plates and jaw plates should be changed before they are fully worn out in order to avoid damage to the crusher components (worn jaw plates imposes unnecessary excessive loads on the crusher).
As shown in above figure, it is recommended that a jaw crusher should not run any longer once the tooth profile of jaw plate has reduced to below 90% of its profile height.
Above figure shows indicative lifetimes of wear parts.
It may be noted that usually the fixed jaw plate wears the fastest (compared to the movable jaw plate, the sliding distance between the crushed particle and the fixed jaw plate is more).
As the wear in the inlet part of the crushing chamber is small as compared to the middle and exit sections, it is recommended to rotation and replacement jaw plates as under:
After a new one-piece jaw plate installation, rotate it when 30% of the tooth profile is worn.
Rotate it a second time when the tooth profile at the bottom of the jaw plate is completely worn. Replace the jaw plate after it is completely worn.
As shown in above figure, in case of two-piece jaw plates, worn out jaw plates are removed from the bottom of the crushing chamber and work hardened upper jaw dies are installed at the bottom of the crushing chamber.
New jaw plates are installed at the top of the crushing chamber.
Above procedure will allow for good work hardening of the manganese jaw plates and maintain the best nip angle for maximum through put.
Carry out lubrication as per Deya Machinery’s recommendation.