Basic information about stone crusher plant
What is Stone Crusher Plant?
A stone crusher plant is one-stop crushing installation, which can be used for rock crushing, construction waste crushing, building materials crushing and other similar operations. It can be stationary plant, or mobile plant.
It reduces the large rocks into smaller ones, gravel, and sand as per requirements.
In mining operations, the crushing plant is for reducing the ore size to prepare for grinding stage, it is useful in meeting the production requirements while keeping capital and operational costs to a minimum.
The fundamental goal for the design of a stone crusher plant
• Meets production requirements
• Reasonable equipment selection meets basic principles
• Operates at competitive cost
• Complies with today’s tough environmental regulations
• Can be built at a reasonable price
What a typical two stages stone crusher plant looks like
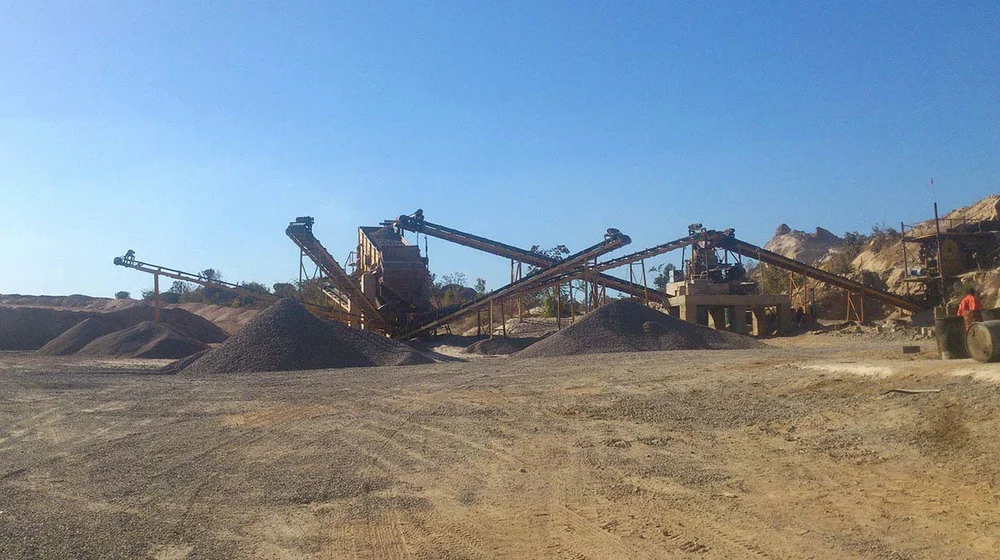
Main equipment of a stone crusher plant
• Feeding equipment, typically vibrating feeder, apron feeder, grizzly feeder
• Primary crushing equipment, typically jaw crusher
• Secondary crushing equipment, symons cone crusher, hydraulic cone crusher, impact crusher
• Tertiary crushing equipment, short head cone crusher, VSI sand making machine, high pressure grinding rolls
• Washing equipment, rotary scrubber, wheel sand washer, screw sand washer
• Connection equipment, belt conveyor
Selection of the crushing equipment
In selecting crushing and screening equipment, the following information should be well considered
• Type of stone, hardness, abrasiveness
• Process capacity per hour
• Maximum feeding size and discharge size
• Expect gravel and sand proportion
• Stationary plant or mobile plant
Typical processing diagram
• Raw materials are loaded to a hopper
• Under the hopper with a grizzly feeder or apron feeder, make sure the raw stones are fed to primary jaw crusher continuously and evenly
• Crushed stones will be sent to the secondary crushing equipment by belt conveyor
• Crusher plant capacity larger than 200 tons per hour should have a tertiary crushing stage, and transfer stockpile is necessary
• The crushed materials from secondary crusher or tertiary crusher are conveyed to vibrating screen for separation
• Screened materials are sent to different stockpiles by belt conveyors
• Sometimes a scrubber washer or sand washer is needed for the production of cleaner gravel and sand
A stone crusher typical crushed size like sand, 3/8’’, 3/4’’, G1, 40mm, etc. It has relation with the C.S.S. size of the crusher, also screen mesh size, this part should be considered when making design. Contact us to customize the stone crusher plant for you.